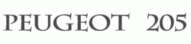
Peugeot 205 Manual
Crankshaft - refitting and main bearing running clearance checkEngine removal and overhaul procedures / Crankshaft - refitting and main bearing running clearance check
Main bearing shell selection XV, XW and XY series engines 1 Bearing shells on these engines are not graded and are supplied in one standard size or one oversize only, to match the dimensions of the respective journal. As the manufacturer’s do not specify an actual running clearance dimension for the bearings, the only safe course of action is to fit new shells whenever an overhaul is being undertaken. Assuming that the relevant crankshaft journals are all within tolerance, the running clearances will then be correct.
2 Note also that from early 1986, the locating tabs of the main bearing shells are offset, and it is not possible to fit the earlier type of main bearing shell to later models with this modification. Seek the advice of a Peugeot dealer or engine overhaul specialist when selecting bearing shells.
XU series engines
3 On some early engines, both the upper and
lower bearing shells were of the same
thickness.
4 However, on later engines the main bearing running clearance was significantly reduced.
To enable this to be done, four different grades of bearing shell were introduced. The grades are indicated by a colour-coding marked on the edge of each shell, which denotes the shell’s thickness, as listed in the following table. The upper shell on all bearings is of the same size, and the running clearance is controlled by fitting a lower bearing shell of the required thickness. This arrangement has been fitted to all engines produced since mid-1994 and, if possible, should also be fitted to earlier engines during overhaul (see paragraph 11).
Bearing colour Thickness (mm)
code Standard Undersize
Upper bearing:
Yellow 1.856 2.006
Lower bearing:
Blue (Class A) 1.836 1.986
Black (Class B) 1.848 1.998
Green (Class C) 1.859 2.009
Red (Class D) 1.870 2.020
Note: On later engines, upper shells are easily
distinguished from lower shells, by their
grooved bearing surface; the lower shells have
a plain surface.
5 On early engines, the correct size of bearing shell must be selected by measuring the running clearance as described under the sub-heading below.
6 On engines produced since mid-1994, when the new bearing shell sizes were introduced, the crankshaft and cylinder block/crankcase have had reference marks on them to identify the size of the journals and bearing bores.
7 The cylinder block reference marks are on the left-hand (transmission) end of the block.
The crankshaft reference marks are on the left-hand (transmission) end of the crankshaft, on the left-hand web of No 1 crankpin (see illustration). These marks can be used to select bearing shells of the required thickness as follows.
13.7 Cylinder block and crankshaft main bearing reference markings - later XU
series engines
A Bar code (used in production) B Identification characters
8 On both the crankshaft and block, there are two lines of identification, a bar code, which is used by Peugeot during production, and a row of five characters (letters and numbers). The first character in the sequence refers to the relevant size of No 1 bearing (at the flywheel/driveplate end) and the last letter in the sequence refers to the relevant size of No 5 main bearing. These marks can be used to select the required bearing shell grade as follows.
9 Obtain the identification character of both the relevant crankshaft journal and the cylinder block bearing bore. Note that the crankshaft characters are listed across the top of the chart, and the cylinder block characters down the side (see illustration).
13.9 Main bearing shell selection chart - later XU series engines
BE Blue (Class A)
NR Black (Class B)
VE Green (Class C)
RG Red (Class D)
Trace a vertical line down from the relevant crankshaft character, and a horizontal line across from the relevant cylinder block character, and find the point at which both lines cross. This crossover point will indicate the grade of lower bearing shell required to give the correct main bearing running clearance. For example, the illustration shows cylinder block reference H, and crankshaft reference 6, crossing at a point within the area of Class D, indicating that a Red (Class D) lower bearing shell is required to give the correct main bearing running clearance.
10 Repeat this procedure so that the required bearing shell grade is obtained for each of the five main bearing journals.
11 Seek the advice of your Peugeot dealer on parts availability, and on the best course of action when ordering new bearing shells.
Note: On early models, at overhaul it is recommended that the later bearing shell arrangement is fitted. This, however, should only be done if the lubrication system components are upgraded (necessitating replacement of the oil pump relief valve piston and spring, as well as the pump sprocket and drive chain) at the same time. If the new bearing arrangement is to be used without uprating the lubrication system, Peugeot state that Blue (Class A) lower bearing shells should be fitted. Refer to your Peugeot dealer for further information.
TU series engines
12 As with the XU series engines described
previously, the TU aluminium block engine
originally had upper and lower bearing shells
of the same thickness, with only two sets of
bearing shell sizes available; standard and
oversize. On aluminium block engines from
mid-1993 onwards, and all cast-iron block
engines, to ensure that the main bearing
running clearance can be accurately set, there
are three different grades of bearing shell. The
grades are indicated by a colour-coding
marked on the edge of each shell, which
denotes the shell’s thickness, as listed in the
following table. The upper shell on all bearings
is of the same size (class B, colour code
black), and the running clearance is controlled
by fitting a lower bearing shell of the required
thickness. This later arrangement should also,
if possible, be fitted to earlier engines during
overhaul.
Aluminium block engine
Bearing colour Thickness (mm)
code Standard Undersize
Blue (class A) 1.823 1.973
Black (class B) 1.835 1.985
Green (class C) 1.848 1.998
Cast-iron block engine
Bearing colour Thickness (mm)
code Standard Undersize
Blue (class A) 1.844 1.994
Black (class B) 1.858 2.008
Green (class C) 1.869 2.019
13 New bearing shells can be selected using
the reference marks on the cylinder
block/crankcase. The cylinder block marks
identify the diameter of the bearing bores and
the crankshaft marks, the diameter of the
crankshaft journals. On early engines, the
correct size of bearing shell must be selected
by measuring the running clearance as
described under the sub-heading below.
14 The cylinder block reference marks are on the right-hand (timing belt) end of the block, and the crankshaft reference marks are on the right-hand (timing belt) end of the crankshaft, on the right-hand web of No 4 crankpin (see illustration). These marks can be used to select bearing shells of the required thickness as follows.
13.14 Cylinder block and crankshaft main bearing reference markings - TU
series engines
15 On both the crankshaft and block there are two lines of identification: a bar code, which is used by Peugeot during production, and a row of five letters. The first letter in the sequence refers to the size of No 1 bearing (at the flywheel/driveplate end). The last letter in the sequence (which is followed by an arrow) refers to the size of No 5 main bearing. These marks can be used to select the required bearing shell grade as follows.
16 Obtain the identification letter of both the relevant crankshaft journal and the cylinder block bearing bore. Noting that the cylinder block letters are listed across the top of the chart, and the crankshaft letters down the side, trace a vertical line down from the relevant cylinder block letter, and a horizontal line across from the relevant crankshaft letter, and find the point at which both lines cross.
This crossover point will indicate the grade of lower bearing shell required to give the correct main bearing running clearance. For example, the illustration shows cylinder block reference G, and crankshaft reference T, crossing at a point within the area of Class A, indicating that a blue-coded (Class A) lower bearing shell is required to give the correct main bearing running clearance (see illustration).
13.16 Main bearing shell selection chart - TU series engines
17 Repeat this procedure so that the required bearing shell grade is obtained for each of the five main bearing journals.
18 Seek the advice of your Peugeot dealer for the latest information on parts availability when ordering new bearing shells.
Main bearing running clearance
check
XU series engines
19 On early engines, if the modified bearing
shells are to be fitted, obtain a set of new
(Yellow) upper bearing shells and new Blue
(Class A) lower bearing shells. On later
(mid-1994 on) engines where the modified
bearing shells are already fitted, the running
clearance check can be carried out using the
original bearing shells, although it is
preferable to use a new set, since the results
obtained will be a lot more conclusive.
20 Clean the backs of the bearing shells, and the bearing locations, in both the cylinder block/crankcase and the main bearing caps.
21 Press the bearing shells into their locations, ensuring that the tab on each shell engages in the notch in the cylinder block/crankcase or bearing cap, and taking care not to touch any shell’s bearing surface with your fingers. There is conflicting information from the manufacturer on the exact placement of the grooved and plain bearing shells, which appears to vary according to engine code and model year.
Also, the bearing arrangement on the project cars dismantled in the preparation of this manual did not conform to the expected placement, but no harm seemed to have resulted. As a general recommendation, if the old bearing shells are being used they must be positioned in their original locations. If new bearing shells are being used on early models, fit the plain shells in all locations that had a plain shell on removal, and likewise for the grooved shells. From mid-1994 onwards, all upper bearing shells are grooved, whereas all lower shells are plain.
22 The running clearance can be checked in either of two ways.
23 One method (which will be difficult to achieve without a range of internal micrometers or internal/external expanding calipers) is to refit the main bearing caps to the cylinder block/crankcase, with bearing shells in place. With the cap retaining bolts tightened to the specified torque, measure the internal diameter of each assembled pair of bearing shells. If the diameter of each corresponding crankshaft journal is measured and then subtracted from the bearing internal diameter, the result will be the main bearing running clearance.
24 The second (and more accurate) method is to use a product known as Plastigage. This consists of a fine thread of perfectly round plastic, which is then compressed between the bearing shell and the journal. When the shell is removed, the plastic is deformed, and can be measured with a specified card gauge supplied with the kit. The running clearance is determined from this gauge. Plastigage should be available from your Peugeot dealer, otherwise, enquiries at one of the larger specialist quality motor factors should produce the name of a stockist in your area.
The procedure for using Plastigage is as follows.
25 With the main bearing upper shells in place, carefully lay the crankshaft in position.
Do not use any lubricant; the crankshaft journals and bearing shells must be perfectly clean and dry.
26 Cut several lengths of the appropriate-size Plastigage (they should be slightly shorter than the width of the main bearings), and place one length on each crankshaft journal axis (see illustration).
13.26 Plastigage in place on a crankshaft main bearing journal
27 With the main bearing lower shells in position, refit the main bearing caps and tighten their retaining bolts to the specified torque. Take care not to disturb the Plastigage, and do not rotate the crankshaft at any time during this operation.
28 Remove the main bearing caps again, taking great care not to disturb the Plastigage, nor to rotate the crankshaft.
29 Compare the width of the crushed Plastigage on each journal to the scale printed on the Plastigage envelope, to obtain the main bearing running clearance (see illustration).
13.29 Measure the width of the deformed Plastigage using the scale on the
card
Compare the clearance measured with that given in the Specifications at the start of this Chapter.
30 If the clearance is significantly different from that expected, the bearing shells may be the wrong size (or excessively worn, if the original shells are being re-used). Before deciding that different size shells are required, make sure that no dirt or oil was trapped between the bearing shells and the caps or block when the clearance was measured. If the Plastigage was wider at one end than at the other, the crankshaft journal may be tapered.
31 If the clearance is not as specified, use the reading obtained, along with the shell thicknesses quoted above, to calculate the necessary grade of bearing shells required.
When calculating the bearing clearance required, bear in mind that it is always better to have the running clearance towards the lower end of the specified range, to allow for wear in use.
32 Where necessary, obtain the required grades of bearing shell, and repeat the running clearance checking procedure as described above.
33 On completion, carefully scrape away all traces of the Plastigage material from the crankshaft and bearing shells, using a fingernail or other object which is unlikely to score the bearing surfaces.
TU series aluminium block engines 34 The procedure is similar to that described in paragraphs 20 to 33, except that the lower shells are fitted to the main bearing ladder instead of the individual bearing caps. On early engines, if the modified bearing shells are to be fitted, obtain a set of new Black (Class B) upper bearing shells and new Blue (Class A) lower bearing shells. On later (mid-1993 on) engines where the modified bearing shells are already fitted, the running clearance check can be carried out using the original bearing shells, although it is preferable to use a new set as described above, since the results obtained will be a lot more conclusive. Note that on most models, all the bearing shells are plain except those fitted to journals 2 and 4 which are grooved. Some engines, however, may have a grooved bearing shell fitted to the upper (cylinder block) location of No 5 main bearing. Fit the ladder, tighten the bolts to the specified torque and carry out the running clearance check.
TU series cast-iron block engines 35 The procedure is similar to that described in paragraphs 20 to 33 except that all the bearing shells are plain except those fitted to journals 2 and 4 which are grooved.
Final crankshaft refitting XV, XW and XY series engines 36 Due to the arrangement of the split crankcase it is necessary to have the pistons, and connecting rods in place in the block before refitting the crankshaft. Carry out the operations described in Section 14, then proceed as follows.
37 Place the bearing shells in their locations as described earlier. If new shells are being fitted, ensure that all traces of protective grease are cleaned off using paraffin. Wipe dry the shells with a lint-free cloth. Liberally lubricate each bearing shell in the cylinder block/crankcase with clean engine oil.
38 Fit the semi-circular thrustwashers which control crankshaft endfloat. The oil grooves of the thrustwashers must be against the machined face of the crankshaft (see illustration).
13.38 Crankshaft thrustwashers - XV, XW and XY series engines
R Oil grooves
39 Oil the shell bearings and lower the crankshaft into position (see illustration).
13.39 Lowering the crankshaft into place
40 Reconnect the connecting rods to the crankshaft as described in Section 14.
41 Fit a new O-ring seal to the crankcase flange and check that the locating dowels are in position (see illustration).
13.41 Crankcase flange O-ring seal
42 Apply jointing compound to the flange.
43 Clean the recesses in the remaining crankcase housing section and fit the main bearing shells. Note that the grooved shells are located in positions 2 and 4.
44 Locate the housing, taking care not to displace the bearing shells.
45 Screw in the ten main bearing/casing bolts with flat washers; noting that the two longer bolts are at the flywheel housing end and the very long one at the crankshaft pulley end on the oil pump side (see illustration).
13.45 Tightening the main bearing/casing bolts
46 Tighten the bolts in the sequence given in two stages to the specified torque (see illustration).
13.46 Main bearing/casing bolt tightening sequence - XV, XW and XY series
engines
47 Now screw in and tighten the seven casing flange bolts with their spring washers (see illustration).
13.47 Refit the casing flange bolts and washers
48 Fit a new crankshaft rear oil seal as described in Part A of this Chapter.
49 Where removed, fit the cylinder head, as described in Part A.
XU series engines
50 Carefully lift the crankshaft out of the
cylinder block once more.
51 Using a little grease, stick the upper thrustwashers to each side of the No 2 main bearing upper location. Ensure that the oilway grooves on each thrustwasher face outwards (away from the cylinder block) (see illustration).
13.51 Fitting the thrustwasher upper segments - XU series engines
52 Place the bearing shells in their locations as described earlier. If new shells are being fitted, ensure that all traces of protective grease are cleaned off using paraffin. Wipe dry the shells and connecting rods with a lintfree cloth. Liberally lubricate each bearing shell in the cylinder block/crankcase and cap with clean engine oil.
53 Lower the crankshaft into position so that Nos 2 and 3 cylinder crankpins are at TDC; Nos 1 and 4 cylinder crankpins will be at BDC, ready for fitting No 1 piston.
54 Lubricate the lower bearing shells in the main bearing caps with clean engine oil. Make sure that the locating lugs on the shells engage with the corresponding recesses in the caps.
55 Fit main bearing caps Nos 2 to 5 to their correct locations, ensuring that they are fitted the correct way round (the bearing shell tab recesses in the block and caps must be on the same side). Insert the bolts/nuts, tightening them only loosely at this stage.
56 Apply a small amount of sealant to the No 1 main bearing cap mating face on the cylinder block, around the sealing strip holes (see illustration).
13.56 Applying sealant to the cylinder block No 1 main bearing cap mating
face
57 Locate the tab of each sealing strip over the pins on the base of No 1 bearing cap, and press the strips into the bearing cap grooves (see illustration).
13.57 Fitting a sealing strip to No 1 main bearing cap
It is now necessary to obtain two thin metal strips, of 0.25 mm thickness or less, in order to prevent the strips moving when the cap is being fitted. Peugeot garages use a special tool, which acts as a clamp. Metal strips (such as old feeler blades) can be used, provided all burrs which may damage the sealing strips are first removed.
58 Where applicable, oil both sides of the metal strips, and hold them on the sealing strips. Fit the No 1 main bearing cap, insert the bolts loosely, then carefully pull out the metal strips in a horizontal direction, using a pair of pliers if necessary (see illustration).
13.58 Using feeler blades to protect the sealing strips as the cap is fitted
59 Tighten all the main bearing cap bolts/nuts evenly to the specified torque.
Using a sharp knife, trim off the ends of the No 1 bearing cap sealing strips, so that they protrude above the cylinder block/crankcase mating surface by approximately 1 mm 60 Refit the centre main bearing side retaining bolts and sealing washers (one at the front of the block, and one at the rear) and tighten them both to the specified torque (see illustration).
13.60 Refit and tighten the centre main bearing side bolts
61 Fit a new crankshaft rear oil seal as described in Part B of this Chapter.
62 Refit the piston/connecting rod assemblies to the crankshaft as described in Section 14.
63 Refit the Woodruff key, then slide on the oil pump drive sprocket and spacer (where fitted), and locate the drive chain on the sprocket.
64 Ensure that the mating surfaces of the front oil seal carrier and cylinder block are clean and dry. Note the correct fitted depth of the oil seal then, using a large flat-bladed screwdriver, lever the old seal out of the housing.
65 Apply a smear of suitable sealant to the oil seal carrier mating surface. Ensure that the locating dowels are in position, then slide the carrier over the end of the crankshaft and into position on the cylinder block. Tighten the carrier retaining bolts to the specified torque.
66 Fit a new crankshaft front oil seal as described in Part B of this Chapter.
67 Ensuring that the drive chain is correctly located on the sprocket, refit the oil pump and sump as described in Part B of this Chapter.
68 Where removed, refit the cylinder head as described in Part B.
TU series aluminium block engines 69 Carefully lift the crankshaft out of the cylinder block once more.
70 Using a little grease, stick the upper thrustwashers to each side of the No 2 main bearing upper location; ensure that the oilway grooves on each thrustwasher face outwards (away from the cylinder block) (see illustration).
13.70 Refitting a crankshaft thrustwasher - TU series aluminium block engine
71 Place the bearing shells in their locations as described earlier. If new shells are being fitted, ensure that all traces of protective grease are cleaned off using paraffin. Wipe dry the shells and connecting rods with a lintfree cloth. Liberally lubricate each bearing shell in the cylinder block/crankcase with clean engine oil (see illustration).
13.71 Ensure each bearing shell tab (arrowed) is correctly located and apply
clean oil
72 Refit the Woodruff key, then slide on the oil pump drive sprocket, and locate the drive chain on the sprocket (see illustration).
13.72 Refitting the oil pump drive chain and sprocket
Lower the crankshaft into position so that Nos 2 and 3 cylinder crankpins are at TDC; Nos 1 and 4 cylinder crankpins will be at BDC, ready for fitting No 1 piston.
73 Thoroughly degrease the mating surfaces of the cylinder block/crankcase and the main bearing ladder. Apply a thin bead of suitable sealant to the cylinder block/crankcase mating surface of the main bearing ladder casting, then spread to an even film (see illustration).
13.73 Apply a thin film of sealant to the cylinder block/crankcase mating
face . . .
74 Lubricate the lower bearing shells with clean engine oil, then refit the main bearing ladder, ensuring that the shells are not displaced, and that the locating dowels engage correctly (see illustration).
13.74 . . . then lower the main bearing ladder into position
75 Install the ten 11 mm main bearing ladder retaining bolts, and tighten them all by hand only. Working progressively outwards from the centre bolts, tighten the ten bolts, by a turn at a time, to the specified Stage 1 torque wrench setting. Once all the bolts have been tightened to the Stage 1 setting, angle-tighten the bolts through the specified Stage 2 angle using a socket and extension bar. It is recommended that an angle-measuring gauge is used during this stage of the tightening, to ensure accuracy (see illustrations).
13.75a Tighten the 11 mm main bearing bolts to the Stage 1 torque setting . .
.
13.75b . . . then angle-tighten them through the specified Stage 2 angle
If a gauge is not available, use a dab of white paint to make alignment marks between the bolt head and casting prior to tightening; the marks can then be used to check that the bolt has been rotated sufficiently during tightening.
76 Refit all the 6 mm bolts securing the main bearing ladder to the base of the cylinder block, and tighten them to the specified torque. Check that the crankshaft rotates freely. On engines with a grooved bearing shell fitted to the upper (cylinder block) location of No 5 main bearing, working on one bolt at a time starting with the centre and working progressively outwards, loosen the 11 mm main bearing ladder retaining bolts, and then tighten to the Stage 3 and then Stage 4 torque wrench settings.
77 Refit the piston/connecting rod assemblies to the crankshaft as described in Section 14.
78 Ensuring that the drive chain is correctly located on the sprocket, refit the oil pump and sump as described in Part A of this Chapter.
79 Fit two new crankshaft oil seals as described in Part A.
80 Refit the flywheel as described in Part A of this Chapter.
81 Where removed, refit the cylinder head as described in Part A. Also refit the crankshaft sprocket and timing belt as described in Part A.
TU series cast-iron block engines 82 Carefully lift the crankshaft out of the cylinder block once more.
83 Using a little grease, stick the upper thrustwashers to each side of the No 2 main bearing upper location. Ensure that the oilway grooves on each thrustwasher face outwards (away from the cylinder block) (see illustration).
13.83 Fitting a thrustwasher to No 2 main bearing upper location - TU series
cast iron block engines
84 Place the bearing shells in their locations as described earlier (see illustration).
13.84 Ensure that the tab (arrowed) is correctly located in the cap when
fitting the bearing shells
If new shells are being fitted, ensure that all traces of protective grease are cleaned off using paraffin. Wipe dry the shells and connecting rods with a lint-free cloth. Liberally lubricate each bearing shell in the cylinder block/crankcase and cap with clean engine oil.
85 Lower the crankshaft into position so that Nos 2 and 3 cylinder crankpins are at TDC; Nos 1 and 4 cylinder crankpins will be at BDC, ready for fitting No 1 piston.
86 Lubricate the lower bearing shells in the main bearing caps with clean engine oil. Make sure that the locating lugs on the shells engage with the corresponding recesses in the caps.
87 Fit the main bearing caps to their correct locations, ensuring that they are fitted the correct way round (the bearing shell lug recesses in the block and caps must be on the same side). Insert the bolts loosely.
88 Tighten the main bearing cap bolts to the specified Stage 1 torque wrench setting.
Once all the bolts have been tightened to the Stage 1 setting, angle-tighten the bolts through the specified Stage 2 angle, using a socket and extension bar. It is recommended that an angle-measuring gauge is used during this stage of the tightening, to ensure accuracy. If a gauge is not available, use a dab of white paint to make alignment marks between the bolt head and casting prior to tightening; the marks can then be used to check that the bolt has been rotated sufficiently during tightening.
89 Check that the crankshaft rotates freely.
90 Refit the piston/connecting rod assemblies to the crankshaft as described in Section 14.
91 Refit the Woodruff key to the crankshaft groove, and slide on the oil pump drive sprocket. Locate the drive chain on the sprocket.
92 Ensure that the mating surfaces of front oil seal housing and cylinder block are clean and dry. Note the correct fitted depth of the front oil seal then, using a large flat-bladed screwdriver, lever the seal out of the housing.
93 Apply a smear of suitable sealant to the oil seal housing mating surface, and make sure that the locating dowels are in position. Slide the housing over the end of the crankshaft, and into position on the cylinder block.
Tighten the housing retaining bolts securely.
94 Repeat the operations in paragraphs 92 and 93, and fit the rear oil seal housing.
95 Fit a new front and rear crankshaft oil seal as described in Part C of this Chapter.
96 Ensuring that the chain is correctly located on the drive sprocket, refit the oil pump and sump as described in Part C of this Chapter.
97 Refit the flywheel as described in Part C of this Chapter.
98 Where removed, refit the cylinder head and install the crankshaft sprocket and timing belt as described in the relevant Sections of Part C.




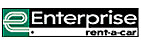
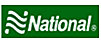

